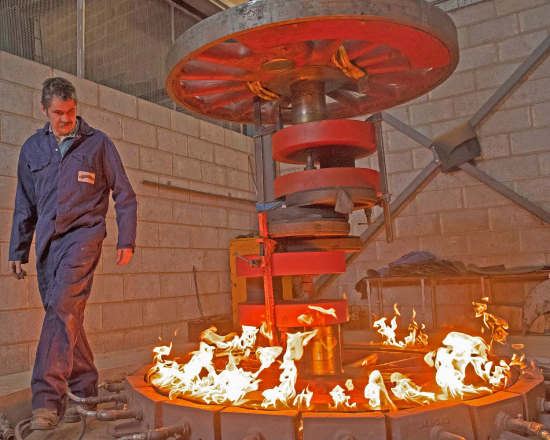
Not Your Average Tyre Change!
Heritage railway engineers at the South Devon Railway (SDR) know only too well that fitting heavy, new steel tyres to a steam locomotive is a lengthy and complex process, and it’s certainly nothing like the average tyre change at a garage which is usually done in minutes!
So, in week one of the six-week long nationwide ‘Love Your Railway’ awareness campaign, whose first theme is ‘Heritage’ this week, here’s how a steam railway tyre is changed in both words and pictures.
Unlike your standard car tyre, these four to six feet diameter wheels take virtually a full day to fit each one and require the use of some heavy-duty, traditional engineering machinery. The SDR can also fit even bigger wheels well over six feet in diameter as well, and smaller ones too.
Most steam locomotive have at least four large driving wheels, and often six, but sometimes eight, plus two or four wheels on ‘pony trucks’ at the front or back!
The tyres are made from top-quality steel sourced from South Africa, which means it can take six to nine months to get the different sizes ordered and shipped to the UK.
In the attached pictures, the re-tyring process is shown whereby the engineers place the machined steel tyre inside a gas-powered hearth. This heats up the metal tyre ring until it’s ‘cooked’ sufficiently so that it expands just enough to then drop the wheel centre into the middle of the tyre very carefully.
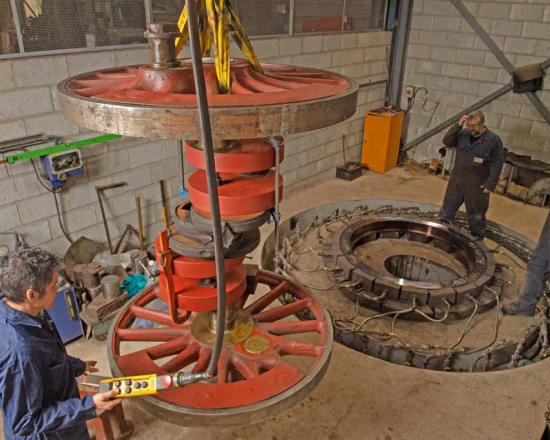
The steel tyre then cools, causing it to shrink to fit the wheel centre tightly and it is then further secured by either using rivets; ‘double nip’ or Gibson ring methods later.
The enduring popularity of heritage railways and steam engines means the engineering team at Buckfastleigh in Devon, have been kept busy even throughout lockdown.
Dick Wood, PR Manager for the South Devon Railway said: “The older, traditional steel railway wheels have a conventional tyre fitted in a similar way to a car. The tyre on the outside is the bit which wears out and eventually needs to be replaced.
“We take the new tyre and heat it steadily in a hearth to the right temperature and size so it expands, and then we can drop the wheel centre in snugly so that it shrinks to fit tightly onto the wheel centre as it cools. It’s a precision process with tolerances roughly the thickness of a human hair.
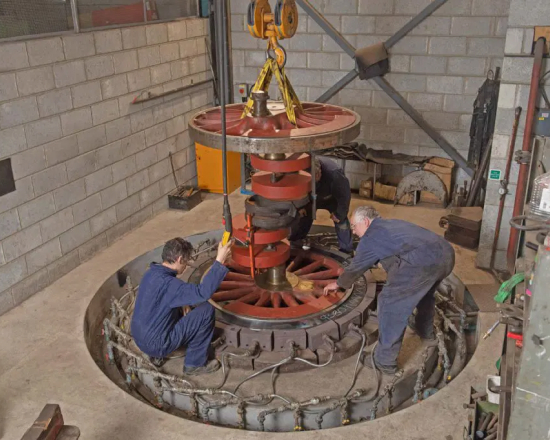
“Then, we finally secure the tyre to the wheel centre using different methods depending on the specification required by the owner. It’s very important for safety that the tyre doesn’t move on the wheel centre.
“It’s a very specialised process and we’ve invested a lot of time, money and expertise to do this heavy engineering work. There are some other companies that do this work too, but we are definitely one of the leading operators of this traditional railway technology.
“And there is plenty of work to go around keeping the country’s steam engines going and older diesel locos on the network fitted with traditional tyres – so far, the SDR’s engineering business reckons to have fitted some 3,000 tyres in ten years!
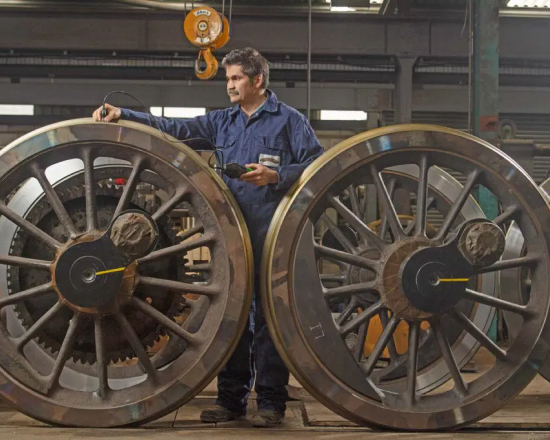
“The big problem all steam loco owners face is simple — the cost of keeping them absolutely up-to-date in order to satisfy stringent safety requirements is going ever higher every year.
“So, most heritage railways like us are lucky if their steam train operations break even, and Covid certainly hasn’t helped us with a £2 Million loss incurred, but thankfully offset by us raising £1.3 Million in donations and Government and Council grants. Our engineering business was the only part of the SDR that worked normally throughout the lockdowns, so that income was vital.
“We feel it’s important to continue and continue to develop the heritage engineering skills we have in place here at the SDR, and so keep them alive for future generations to enjoy steam trains for another 100 years hopefully.”
Images courtesy of Bournemouth News & Picture Agency.